
How the Mossman Mill's bio-refinery will work in the future
AGRICULTURE
The recent acquisition of the Mossman Mill by Far Northern Milling (from Mackay Sugar) and the plan to create a Daintree Bio Precinct (DBP) has been both welcomed and viewed as a significant boost for Mossman and the Douglas Shire as a whole.
To obtain a better understanding of what this means to the future of the mill, Newsport put the following questions to Rajinder Singh, Deputy Chair of FNM and Deputy Chair of Daintree Bio-Precinct Ltd.
Mr Singh is also a Director of Canegrowers Tableland and the district’s representative on the Canegrowers Policy Council. He is a member of the Queensland Cane Growers Organisation Ltd (QCGO) Board.
Part of a family farming operation growing 70,000 tonnes of sugarcane on the Tableland and in the Mulgrave area, he has a Bachelor of Engineering from University of Queensland and a strong interest in research and development.
His farming business is accredited in Smartcane BMP, the industry’s best management practices program.
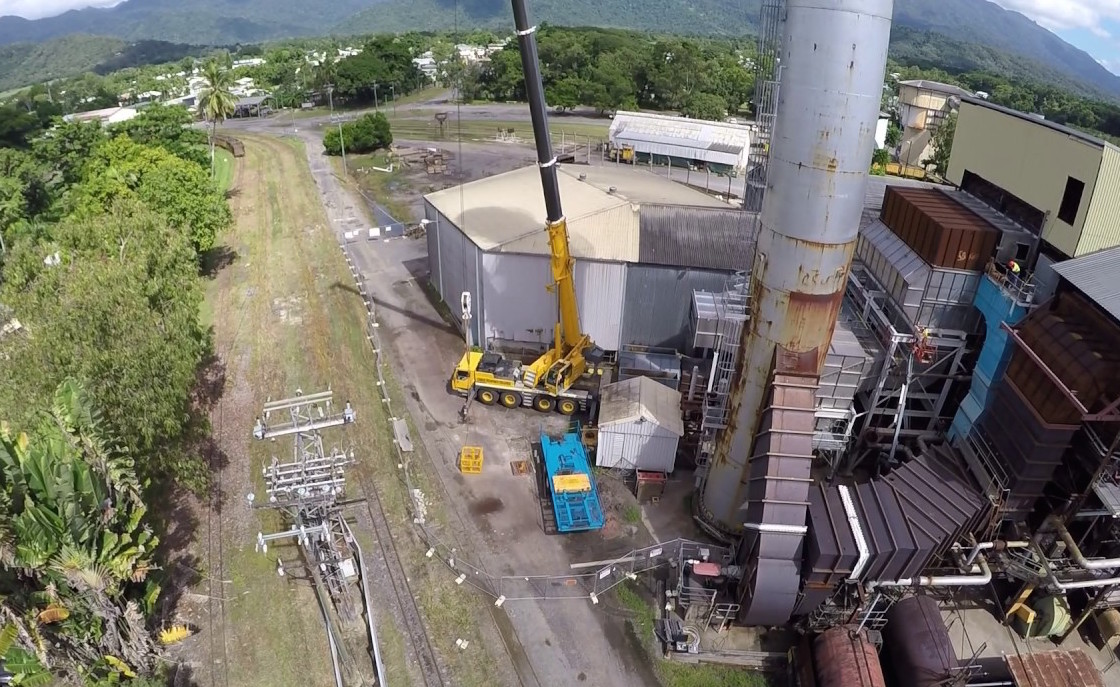
Newsport: What does a bio-refinery mean for the sugar cane industry, and for a mill, eg its purpose, value-add?
Singh: A sugarcane bio-refinery is an integrated processing facility capable of producing multiple high value products from the sugarcane plant. Sugarcane is a highly efficient C4 photosynthetic crop producing high yields of biomass on an annual basis.
Until recently, sugar mills, including Mossman, have focused almost exclusively on the sucrose sugar component. This makes up more than 90% of current revenue. Molasses sold for stockfeed makes up the bulk of the remainder. The other two co-products, bagasse and mill mud, generate little or no revenue.
While bagasse is used to generate the power and steam requirements of the mill during the crushing season, it remains a vastly underutilized resource.
Sugar mills as a bio-refinery have the advantage of existing infrastructure and transport systems to process large quantities of biomass in a central location.
The outputs of a bio-refinery are wide ranging:
- High value food grade products derived via fermentation of sucrose. This includes vitamins, nutraceuticals, flavours, low and zero calorie sweeteners, as well as beer and spirits;
- Pharmaceuticals, cosmetics and moisturizers produced via fermentation of sucrose;
- Fuel alcohols such as ethanol, methanol and butanol;
- Renewable energy generation including electricity, steam, biogas and hydrogen; and
- Green chemicals as a replacement for petrochemicals in the manufacture of everyday products such as plastics, apparel, and moulded engineering components.
N: The creation of a bio-refinery in Mossman is expected to provide a viable future for the mill and long-term economic benefits. Can you outline the types of economic benefits?
S: Relying on 90% of revenue from sugar that is priced on a very volatile NY No11 futures market means that Mossman Mill will struggle to survive.
A bio-refinery approach to business will add more value to all components of the sugar cane plant and create a broader range of products. The key is to produce products that have a more stable pricing structure.
Mossman Mill is a small sugar mill and so the focus will be on producing low volume high value products.
The proposed value adding activities will significantly increase the value of products produced.
N: The bio-refinery (in Mossman) will use the latest in green chemical technology and will also diversify the Douglas Shire economy through the introduction of a considerable number of green chemical manufacturing jobs. What types of jobs will be created? Can you expand on green chemical technology?
S: The manufacturing process involves fermentation of sugar, a well-known and proven technology.
In recent decades there has been a lot of R&D aimed at producing cellulosic sugars from biomass as a potential lower cost source of sugar. Fermentation will work with cellulosic or natural sugars. However, the cost of cellulosic sugars is still too high. For high value chemicals using sucrose or glucose is still a viable and easier option.
Fermentation uses a product specific microbe that consumes sugar to produce the desired product.
Therefore the yeast strain that turns sugar into ethanol will only produce ethanol.
To produce a particular green chemical the R&D effort has been on creating a new strain of yeast or other microbe that produces that particular product. Significant advances in bio-technology have led to major advances in the health, food & beverage sector as well the industrial manufacturing sector.
Fermentation will require a different set of skills. It will broaden the skill set required in the local workforce. In terms of skill it is similar to sugar milling and processing where specialised skills and knowledge are also required.
N: Once up and running, and speaking traditionally, would a bio-refinery operate 12 months a year?
S: To ensure efficient use of capital, the aim is to have value adding operations run year round. However, this will be determined by the availability of feedstock.
Practically the harvesting and initial processing of sugarcane will remain seasonal.
Harvesting cannot occur during the wet season. Sugarcane is an annual crop and cane that is harvested after mid-November doesn’t yield well the following year. Therefore the ideal harvesting season has been from June to November.
With a bio-refinery there is potential in the future to lengthen the harvesting season by starting a little earlier. The focus may change from maximising sugar production to maximixing biomass production.
Sugar, bagasse and molasses can be stored to allow year round value adding.
N: Traditionally, how long does it take to set up a bio-refinery? And what does it cost (estimate is fine)?
S: This will depend on the product, the scale of the plant and how long the technology has been operating at commercial scale. With new products that have only recently reached commercial stage the time to start up is 3+ years.
Capex (capital expenditure) also depends on the product and the maturity of technology required. It typically ranges from $150m to $200m. The processing that is required after fermentation (separation and purification) tends to be specific to the particular molecule.
N: When will a mill, such as Mossman, start seeing the results of the bio-refinery?
S: DBP with the assistance of experts is currently engaged in an options selection process.
Prior to this there has been considerable work done on green chemicals. This remains a possible longer term high value, high capex option.
DBP needs to ensure that it is not highly dependent on a single option and that it has thoroughly examined all possible options.
The options selection process will come up with processes and products that will provide returns in the short, medium and long term. It is also important that the options selected are the best possible fit for Mossman.
Mossman will start seeing results within three years.
N: Are bio-refineries meant to decrease marketplace risk for many technologies?
S: There will always be some market place risk. New technology always has the potential to disrupt existing business to the point of extinction.
Bio-refineries use sustainable renewable feedstock. Although not wanting to pay a premium, consumers are increasingly demanding products that are manufactured using such feedstock.
Reducing greenhouse gases to stem the increase in global warming is becoming an important goal for many. A circular economy where goods are recycled at end of life is also important. Therefore as an example, products that use compostable or recyclable plastics are preferred.
In the case of green chemicals a significant difference with petrochemicals lies in the impurities of which there is always a small quantity. Petrochemicals contain impurities which are often carcinogenic or irritating whereas the impurities associated with green chemicals are not.
For consumers this is very important in products such as cosmetics and moisturizers Consumers are willing to pay a premium for these.
N: What goes into the physical design of a bio-refinery?
S: Converting sugar albeit sucrose or cellulosic sugars from biomass such as bagasse into a food product, biofuel or a green chemical requires fermentation as the first step.
This is then followed by separation of the product from the fermentation broth.
The final phase involves evaporation and distillation to produce the purified product.
Any waste produced during the process can put through an Anaerobic Digester to produce bio-gas. This can then be used to produce electricity, steam, or CNG (compressed natural gas).
Join the conversation
Give a THUMB UP or THUMB DOWN on what we've covered OR place a COMMENT below.
Got a great news tip or video? We'd love to see it.
Send news tips to editor@newsport.com.au
* Readers are encouraged to use their full details below to ensure comment legitimacy. Comments are the opinions of readers and do not represent the views of Newsport or its staff. Comments containing unlawful, obscene, defamatory, personal or abusive material will not be published.